Direct Rolling Scheduling (DRS) can be leveraged to resolve the scheduling complexities at the caster and rolling mill both for Endless Strip Production, Compact Strip Production and the traditional steel plant. It works like a charm.
Direct rolling is the process of producing coils without intermediate storage of the slabs: The produced slabs are immediately rolled while they are still hot. Generating direct rolling schedules is a challenging task as conflicting scheduling rules applied at the caster and the mill create problems. A solution in which the caster or mill schedule are generated first and then propagated to the mill will inevitably lead to sub-optimal results. To resolve this problem, the casters and the mill must be scheduled simultaneously.
This solution allows for direct rolling on Endless Strip Production (ESP) lines, Compact Strip Production (CSP) lines and direct charging in a traditional integrated steel plant (ISP).
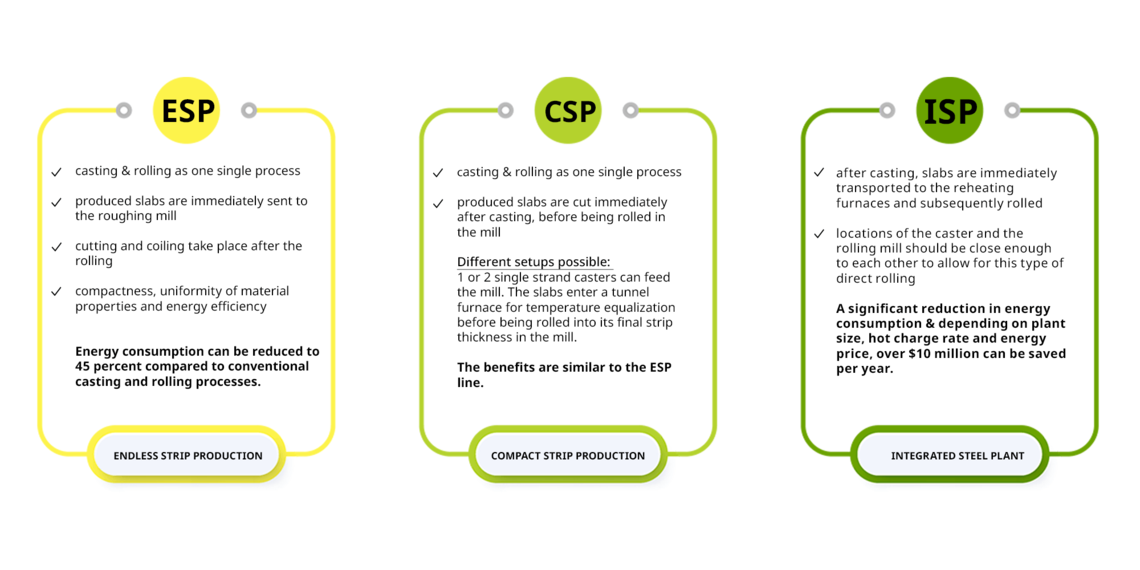
Scheduling problems associated with direct rolling of steel
For direct rolling, these sequences are identical. Each sequence consists of one or more tundishes on the caster(s) (one per caster), which correspond with one rolling sequence on the mill.
Conflicting process constraints on the caster and the mill complicate this process. Casters operate in batches of single grade heats. A variety of process constraints must be respected like width and grade change rules, tundish wear etc. Mill sequences also have to respect completely different - and often conflicting - process constraints.
Available solutions solve these scheduling problems in isolation. Instead, an integrated approach is required, in which schedules are generated for both the caster and the mill at the same time.
A scheduling solution with direct rolling scheduling of steel
PSImetals Direct Rolling Scheduling is a standard component of PSImetals family of planning and scheduling solutions for the metals industry. The solution is designed to generate direct rolling sequences while respecting all constraints that apply on both the caster and the mill simultaneously. Sequences are generated one by one. One run of the algorithm creates one sequence. DRS offers all the necessary visualization tools to analyze the order population, introduce rules and constraints, and validate the results. The system also offers flexible report generation as well as customizable KPI calculation and visualization.
The main input to the system consists of a list of production orders which contains all the information required to produce the coils ordered by a customer such as due date, coil dimensions etc. DRS implements a prioritization mechanism to define which orders to produce first. This prioritization takes into account the due date and a selected order category pre-defined by the user. Other inputs to DRS include grade information, caster information, caster scheduling rules, rolling mill scheduling rules and tuning parameters.
In pursuit of a near-optimal solution, the algorithm evaluates a large number of feasible solutions. Such evaluation assists in applying a global objective function to a candidate solution. The objective function must reflect the quality of the solution for both the caster(s) and the rolling mill.
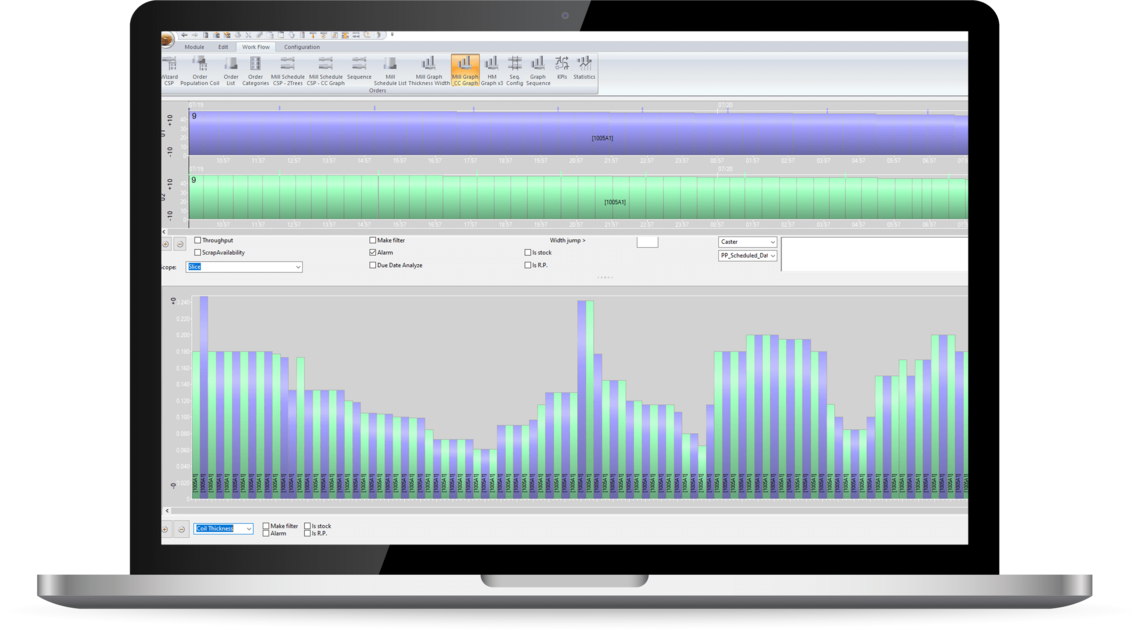
The operator can also edit results, as various tools are available to support this process in a user-friendly way. Changes made by the user to one sequence are automatically reflected in the other sequence. This propagation enables the user to maintain the feasibility of the overall sequence at all times.
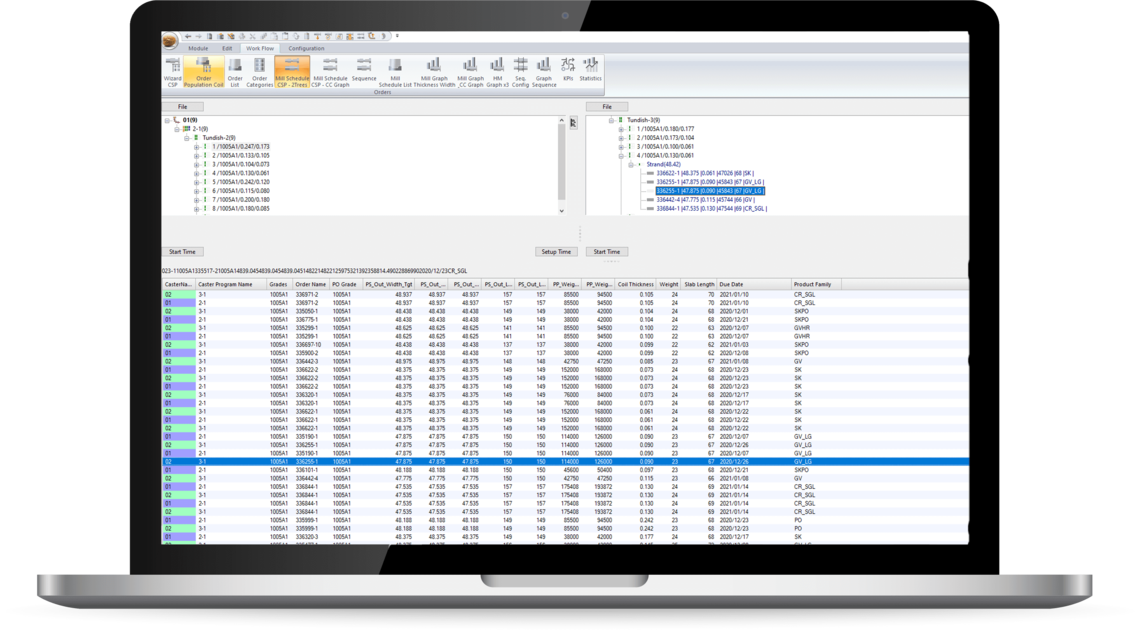
Get your steel plant started with direct rolling scheduling
Although there are significant business benefits of direct rolling, caster, hot mill synchronization, production constraints and process restrictions make achieving these benefits difficult. Often, they are only partly realized through a manually intensive process.
DRS has been designed with a high degree of configurability and genericity in mind. Both data and user interfaces can be adapted to any site-specific configuration without requiring any extra development work. More importantly, the advanced algorithm that is the heart of DRS can be controlled through a comprehensive set of tuning parameters and configuration settings. Therefore, DRS could be deployed in any CSP or ESP plant looking for intelligent software support to implement direct rolling scheduling.