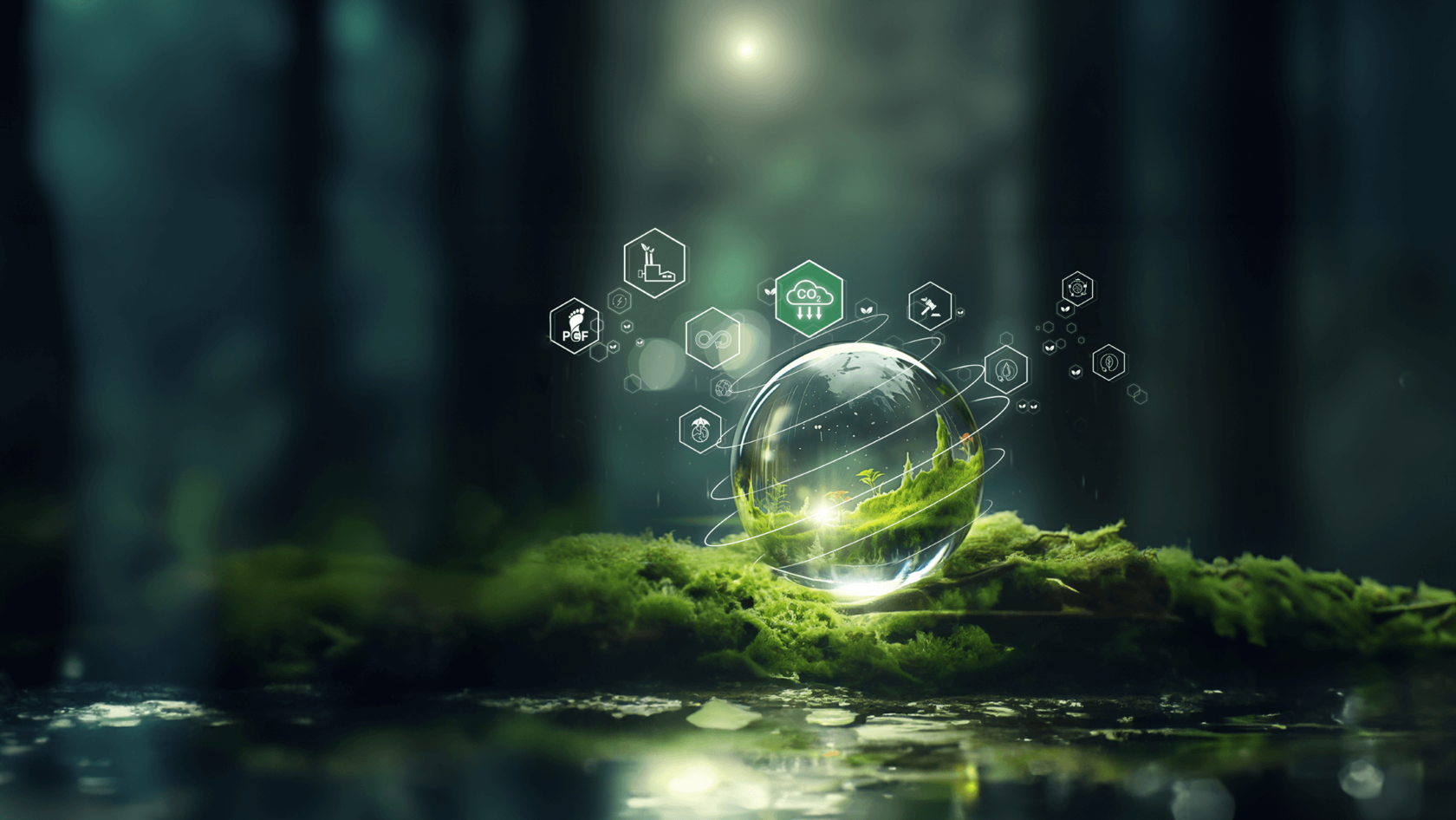
The PSImetals Production Execution System (PES) can be configured and used to transparently calculate and track emissions on piece and product level along the entire production chain, from iron and steelmaking, through hot and cold rolling, to finishing lines. This provides a “Cradle-to-Gate” Product Carbon Footprint (PCF), which steel producers can pass on to their customers as an additional quality KPI.
Challenges
The market is increasingly demanding reliable carbon footprint calculations and certificates for the various metals products.
In the general approach of mass balance-based CO₂ equivalent accounting, the calculations are still not broken down to individual products but are instead based on annual production tonnage and average CO₂ equivalents for different plant areas.
Granular CO₂ equivalent accounting
Tracking of emission-relevant material and energy consumptions based on primary process data for each production step of a specific product. Appropriate allocation of related emissions to the product, by-products, and scrap parts used in other productions.
"Cradle-to-Gate" accounting of emissions
PSImetals MES tracks and calculates greenhouse gas emissions from the preparation and charging of raw materials throughout the entire production chain, up to commissioning for shipment to the customer. This includes Scope 1, Scope 2, and upstream Scope 3 emissions, where specific emission data from energy and raw material suppliers are also required.
Accounting for lump-sum emissions
Global emissions, e.g. from idle times or preparations of next production campaigns, which cannot be assigned to a single product after its treatment in a specific production step, must be considered as lump-sum contributions to be evaluated from a mass balance per kg of produced steel.
Usage scenarios
The PCF tracking workflow allows users to manage CO₂ emissions by maintaining master data and defining rules to calculate emissions at each production stage. Emission values are stored and easily retrieved via an API for reporting and analysis.
Common PCF tracking workflow
The common PCF tracking workflow represents a sequence of processes with input and output for each process as well as a trigger initiating the process execution.
Master data maintenance
CO₂ emission accounting is based on the description of all factors influencing emissions at each stage of production, including single material processing, installation-related idle times, area-related factors, and more. A system administrator manually maintains this data using PSImetals screens. Users can define rulesets for CO₂ emission calculations according to the production stage and the available data. These rulesets are stored in what are known as Process Specifications.
Production booking and process snapshot creation
After receiving a production report, e.g. from a process automation system, PSImetals triggers production booking and creation of a Process Snapshot – a special data container linked to a Material Genealogy node. The process uses as input the data from the production report message. The output of this process is a storage of all specified details related to produced material and production process itself within Process Snapshot - including CO₂ emission related data. CO₂ emission calculation is triggered according to ruleset specified in according Process Specification. Calculated CO₂ emission values are also stored in Process Snapshot and visualized in GUI of related Material Genealogy node.
Provision of co₂ emission values
A special API allows requesting actual CO₂ emission values for selected material in simple form without deep knowledge of PSImetals data structures. A reporting tool can use this API for getting CO₂ emission values for report generation.
Benefits
-
Real-time tolerance monitoring
Continuously checks emissions data against predefined tolerances during production.
-
Material genealogy integration
Tracks emissions along the entire Material Genealogy for comprehensive visualization and reporting.
-
Enhanced product certification
Integrates PCF data into product certificates for proof of fulfillment of customer requirements.
-
Optimized green steel production
Tracked PCF data can be used to forecast carbon emissions and guide green steel production.
Conclusion
Based on configurable Quality Process Snapshots, the PSImetals Product Carbon Footprint (PCF) accounting approach offers transparent calculations and tracking of energy consumptions and CO₂ emissions at both piece and product levels throughout the entire production chain. It monitors all emission-relevant process data for each product in real-time and calculates Scope 1, Scope 2, and upstream Scope 3 CO₂ emissions, providing “Cradle-to-Gate” PCF tracking.
Products used
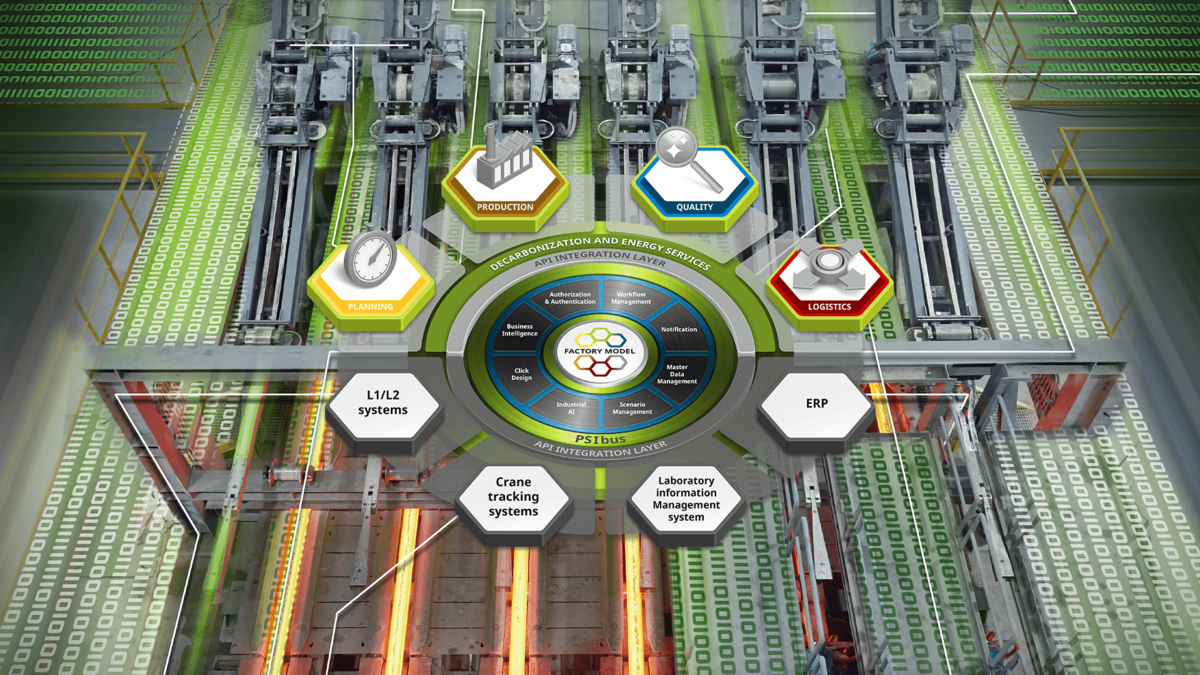
PSImetals
As a manufacturer of steel or non-ferrous products, you ensure your competitive edge by delivering the products to your customers in the agreed quantities and qualities as well as on schedule. PSImetals is the software product based on which we deliver production management solutions for the metals industry and support you in meeting the demands of your customers.
-
Process flow optimization
PSImetals optimizes and balances process flows and resource usage.
-
Efficient KPIs
PSImetals uses efficiency KPIs as optimization targets.
-
Reduced cost
PSImetals enhances cost effectiveness which increasingly implies sustainability.
![[Translate to Polski:] PSImetals-Service-Platform [Translate to Polski:] PSImetals Products-Module werden in der Serviceplattform angezeigt.](/fileadmin/_processed_/6/9/csm_PSI_Virtual_Factory-SP_fbc6e6659b.png)
PSImetals
Zoptymalizuj produkcję metali dzięki SCM, APS i MES. PSImetals to oprogramowanie, na którym opierają się nasze rozwiązania do zarządzania produkcją dla przemysłu metalowego.
-
Optymalizacja przepływu procesów
PSImetals optymalizuje i równoważy przepływy procesów i wykorzystanie zasobów.
-
Wydajne wskaźniki KPI
PSImetals wykorzystuje kluczowe wskaźniki wydajności jako cele optymalizacji.
-
Obniżone koszty
PSImetals zwiększa efektywność kosztową, co w coraz większym stopniu przekłada się na zrównoważony rozwój.
FAQs
How does PCF by PSImetals consider scrapped parts during production process?
PSImetals manages the scrap lifecycle within the plant: so when scrap occurs during production, scrap material is created which inherits its portion of PCF. When the scrap is charged into EAF or BOF, the PCF backpack is added to the new heat. However, guidelines should be defined by regulating authorities. PSImetals can also work with gross and net PCF values and is flexible with the rules configuration.
How does PCF by PSImetals take into account emissions not related to specific materials in a production line?
It is possible to define lump sum emissions at the production line and area level that are not part of the detailed production order steps of a specific material. An example of this would be production preparation or idle times with no material in the line. This can be evaluated from historical data of the consumptions that cause emissions at a certain period and the amount of steel produced during this period in the respective area.
How does PCF by PSImetals communicate with the involved automation and ERP software systems to exchange the required process and calculated PCF data?
PSImetals uses standard interfaces to exchange messages with the process automation layer, such as production reports containing the consumed electrical energy, gas and raw material amounts. It also communicates with the ERP system in this way, for example, through reports containing the CO₂ emissions calculated per production step and aggregated over all steps so far.