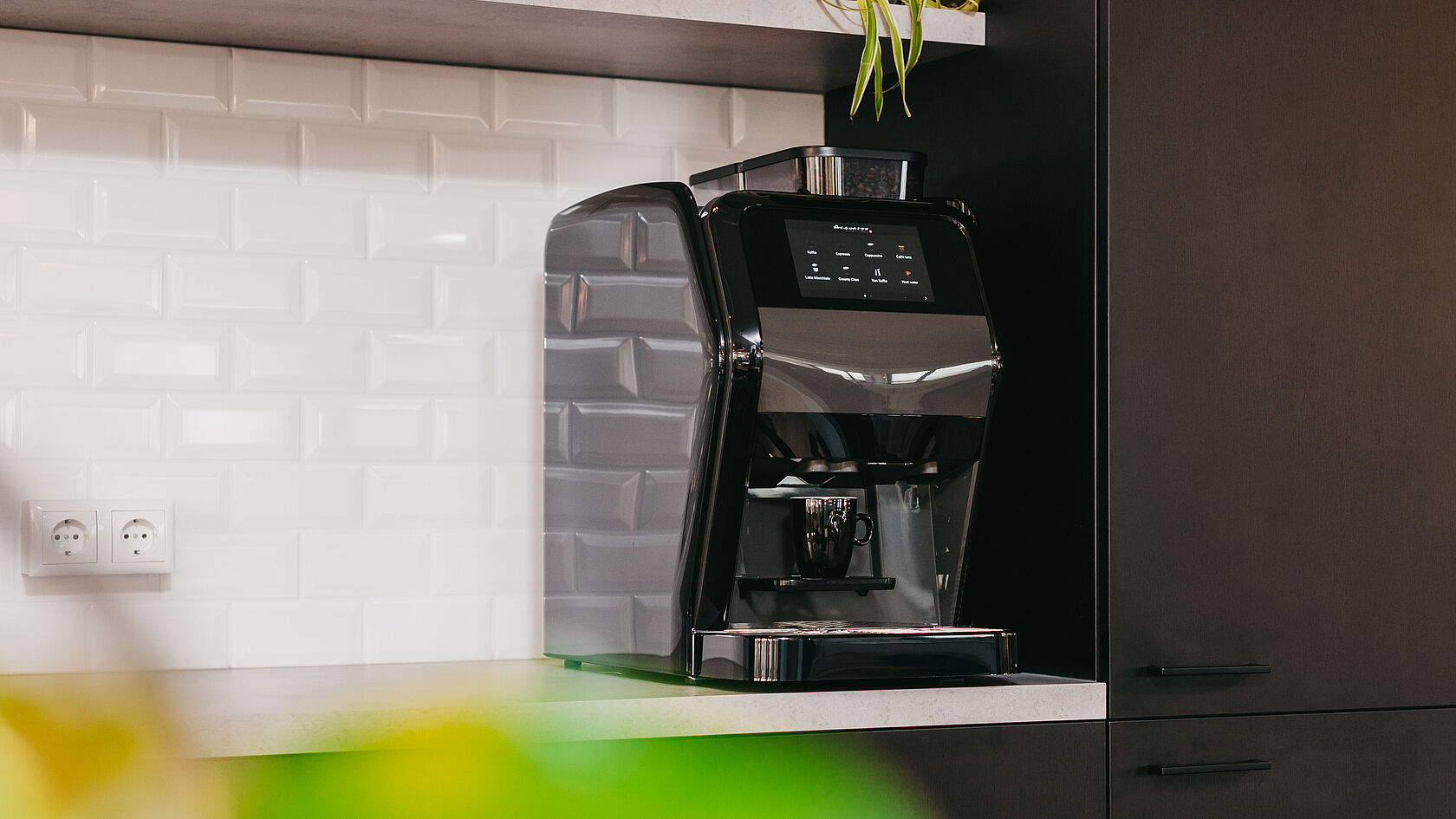
Case Study Aequator reduces throughput times thanks to precise planning
The Swiss coffee machine manufacturer uses the ERP and MES solution to produce small series and even one-offs - with a high degree of automation.
Aequator produces coffee machines to customer order - both one-offs and small batches. In order to achieve short throughput times despite the large number of variants, precise planning and close integration of production and development are essential. The manufacturer solves these and other challenges with a high degree of automation and a sophisticated IT system, the heart of which is PSIpenta/ERP + MES.
About Aequator AG
Aequator has been developing and producing coffee machines since 1933. While the company started out with portafilter machines, today it produces around 15,000 high-quality fully automatic machines and private label machines every year. These are used, for example, in the catering industry, in reception areas, canteens and hairdressers, in hotel breakfast rooms, bakeries and convenience stores.
Challenges
As Aequator produces both small batches and one-offs, this results in a huge range of variants with high demands on multi-stage planning, production and on-time delivery. At the same time, the company is undergoing a major process of change and has to adapt both its product range and its organizational structures in order to tap into new markets.
Production features
- Production of small series and one-offs
- High number of variants
- multi-layered planning processes
- Use of the "one-piece flow" working method (lean production)
- Around 15,000 fully automatic coffee machines per year
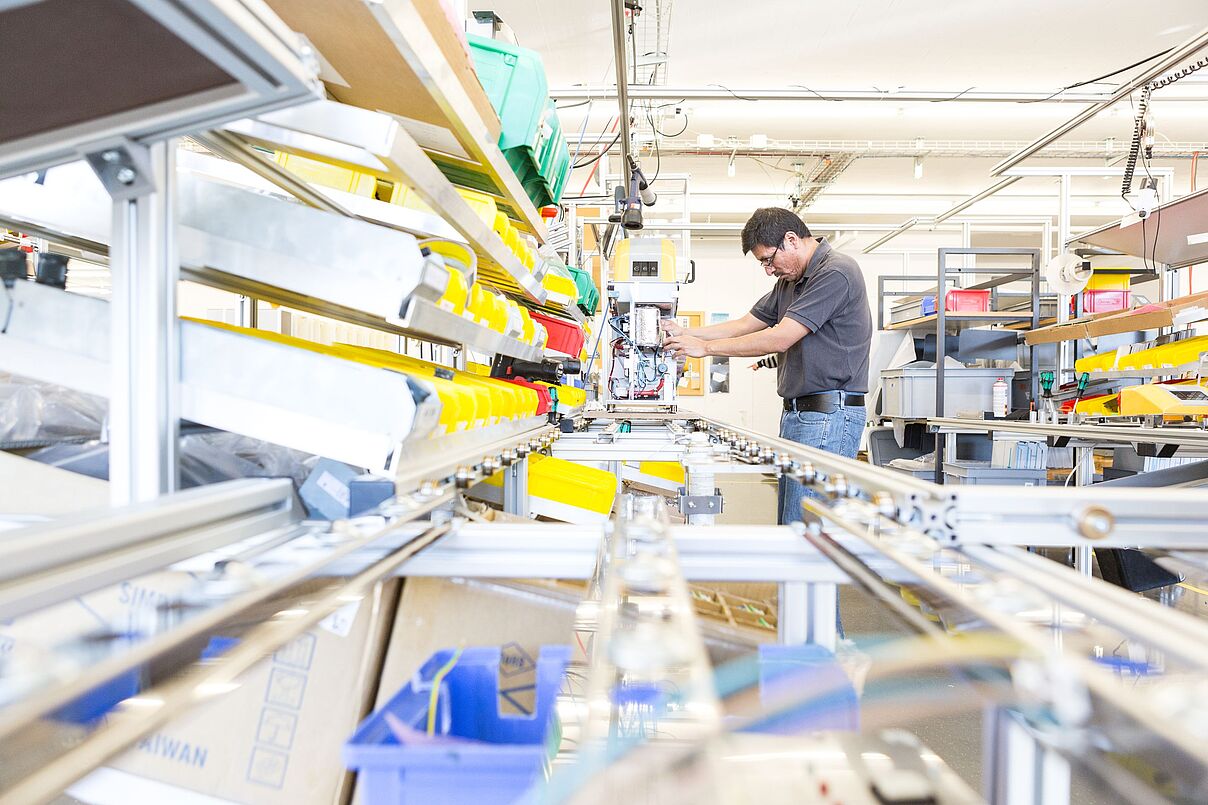
Objectives
Aequator was looking for an end-to-end ERP-MES solution that would support a high number of variants as well as multi-stage production, preferably as standard. On the one hand, the system should efficiently map planning and production processes for one-offs as well as small batches without retooling on the production line and, on the other hand, offer flexible structures as a basis for easy adaptability to changing markets.
Solution approach
The linchpin of production planning and control is the ERP MES system PSIpenta and an integrated, electronic KANBAN system. Together, the software supports the coffee manufacturer in the operational processing of customer orders across the entire supply chain. In addition to order management, variant management and the control station play a key role in the flexible planning processes. Last but not least, the interfaces to development and accounting and the resulting integrated company processes offer great added value.
Implementation
For each product group, Aequator assembles the machines on different production lines in a "one-piece flow". This is a lean production method that is logistically based on flow production, but uses semi-autonomous group work or job rotation to organize the work. Aequator produces up to ten different machine variants and up to seven customer variants on certain production lines.
Order management transmits the customer orders to the control station, which converts them into production orders and lists them in the sequence of their production time. Depending on the selection of resources, the control station then adapts the production time for each order and visualizes the processing status. This also shows when orders are expected to be completed and whether promised delivery dates will be met. As the control station is also available at the assembly lines, the line manager can start, interrupt or stop orders. Once the production order has been completed, the material is booked into the ERP system and the machines are reported as finished. The booking to the warehouse or dispatch warehouse is carried out by the logistics department.
Aequator also benefits from the flexibility of the system with regard to its own change process. The ERP system provides a reliable data basis for the individual processes, which can be flexibly and easily adapted to changing conditions.
The result
Thanks to the sophisticated planning system, Aequator produces coffee vending machines in small batches up to batch size 1 - without time-consuming retooling on the production line - efficiently and on time. The manufacturer can react very flexibly and reliably to customer requests - also because the current capacity utilization situation is displayed clearly and transparently for all employees at all times.
Conclusion
As a contract manufacturer of high-quality products, Aequator AG places high demands on IT and the automation of everyday tasks. The PSIpenta ERP-MES solution meets these requirements and creates the basis for the necessary flexibility and adaptability. In harmony with the accompanying IT solutions, the traditional Swiss company is ideally equipped to continue its long success story in the world of coffee machines.