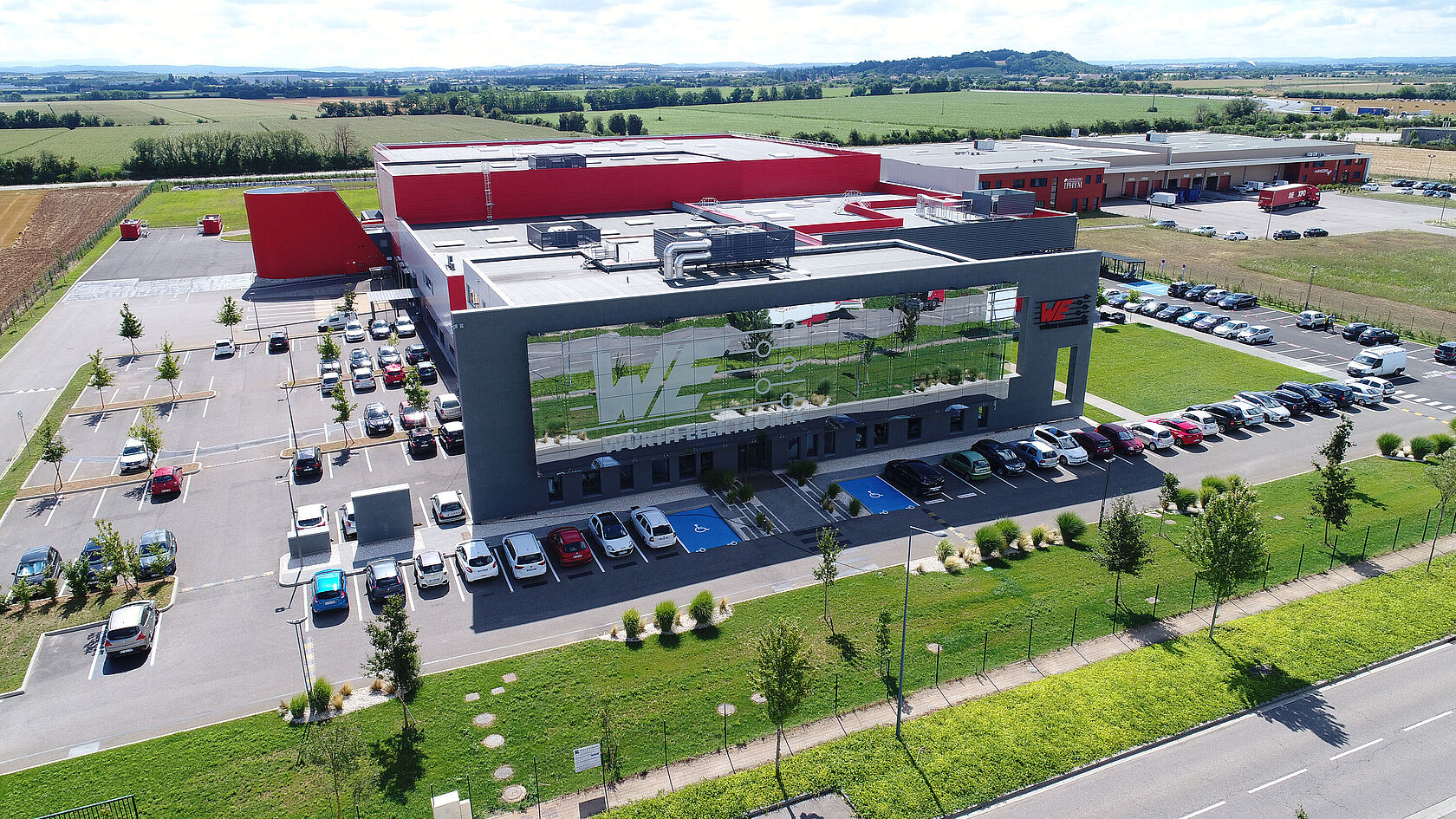
Case Study Efficient logistics automation at Würth Elektronik eiSos
Optimized logistics processes through automation and PSIwms in the central warehouse of Würth Elektronik eiSos.
Würth Elektronik eiSos, headquartered in Waldenburg, Germany, develops, manufactures and markets electronic and electromechanical components for the electronics industry. As one of the largest European manufacturers of passive components, the company is active in 38 countries with direct sales. The product range includes power modules, digital isolators, sensors, connectors, switches and buttons.
Mastering challenges
In order to keep up with fluctuating demand and the company's growth, the technologies and processes at the Waldenburg distribution center must be as scalable as possible. For example, changes in order structure and order numbers must be easily reflected. At the same time, the high demands for fast and error-free order processing require optimal coordination of the logistics processes. Cross-location control of warehouse processes is also becoming increasingly important.
Customer's objective
Solution approach
Würth Elektronik eiSos optimizes its internal logistics processes with the warehouse management system PSIwms. A central element is the integrated forklift control system (FCS) “Transport Control”, which controls transport orders and enables route-optimized processes for the forklifts. The highly dynamic conveyor technology controlled by PSIwms ensures a fast and efficient material flow. It seamlessly connects incoming goods, shuttle warehouse, picking stations, packing stations, and outgoing goods. At a total of 20 stations, the system guides employees through the picking and shipping processes with user-friendly interfaces and ensures a smooth workflow.
Another key advantage of PSIwms is the optimized shipping process. Based on the order and item data, the system determines a shipping-optimized packing scheme for the work orders, controls their circulation and automatically initiates the printing of individual shipping labels.
The interactive warehouse visualization also provides a comprehensive overview of the storage bins. These can be displayed according to fill level or reservation blocks, for example. At the same time, moving objects such as forklifts or load carriers can also be tracked precisely.
Thanks to the multi-site capability of PSIwms, it is also possible to coordinate inventory management and order processing for replenishment across all locations. The partially automated warehouse at Würth Elektronik France in Lyon is also efficiently controlled and integrated into the central order processing system.
Warehouse characteristics
- 11,180 sqm of storage area
- up to 200,000 storage positions
- 9 aisles shuttle warehouse with 38 levels
- 99 level-changing shuttles, 2 double gondola lifts
- 12 CEP goods receipt stations
- 20 fully automated order picking stations; incl. special order picking stations for ESD articles (electrostatic discharge)
- 16 packing stations
- Control of 27 dispatch lanes depending on the shipping mode
- Special storage for moisture sensitive articles (different temperature zones)
- Re-reeling (in conjunction with rolled goods)
- Automatic goods receipt via measuring tunnel (2D barcodes)
The result in detail
The fully automated distribution center in Waldenburg is considered by the company to be a demonstration plant for individual customer requirements and a high level of service, thanks to its state-of-the-art shuttle and Industry 4.0 implementations.
After the latest expansion phase, almost 4,400 pallet locations are available for storing around 30,000 items in the forklift operated high bay warehouse (HBW) and around 200,000 container locations in the small parts shuttle warehouse, which has been expanded to nine aisles. At the same time, the number of processing stations for CEP deliveries in the receiving area was doubled from four to eight.
The intelligence of our logistics processes clearly lies in PSIwms. The system's sustainability offers us long-term investment security. This is a strong basis for future developments.
PSIwms functions in use
- Pick-by-light, automatic test, batch management
- Multi-level packaging units, value-added services
- Adaptive scenario management, archive
- Multi-storage capability (interaction between locations in Waldenburg, Germany und Lyon, France)
Conclusion
In order to meet the increasing demands for efficiency, flexibility and scalability, Würth Elektronik eiSos relies on state-of-the-art automation technologies and a high-performance warehouse management system (PSIwms) at its distribution center in Waldenburg. The optimization of logistics processes through intelligent control, automated conveyor technology and interactive warehouse visualization enables fast, error-free order processing and cross-location coordination. The continuous expansion of warehouse capacities and the use of Industry 4.0 technologies make the distribution center a showcase for customer-oriented logistics and high service quality.