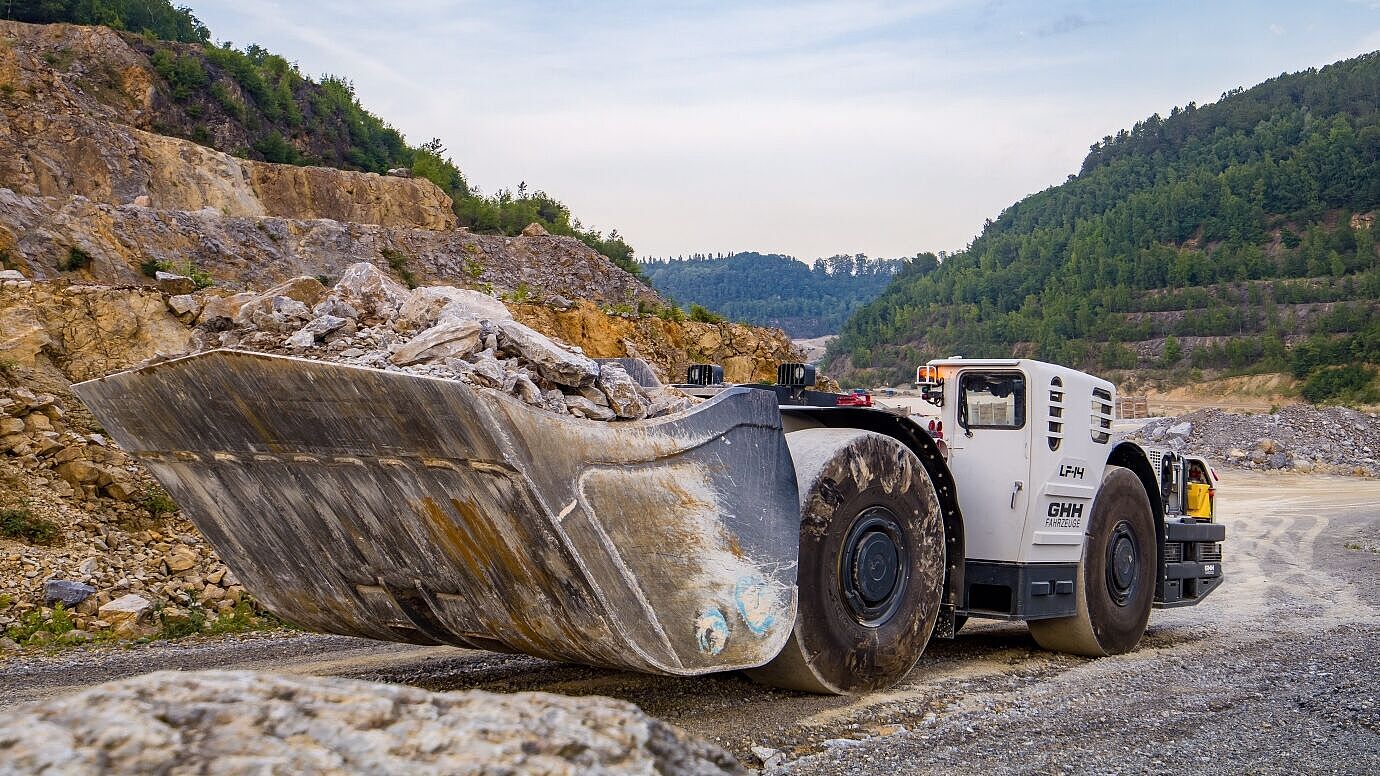
Case Study GHH Fahrzeuge increases data and process quality with PSIpenta
Thanks to PSI's ERP and MES solution: mapping of growing parts lists and data acquisition at the same time as the physical process.
As a classic assembly company, GHH has to manage and orchestrate data of enormous dimensions. The company often has to start production and assembly while adjustments are still being made in development. By introducing the industry standard PSIpenta/ERP and MES including industrial apps, the company has massively increased its data and process quality and benefits from a high level of informative value as well as a high level of acceptance among all users.
About the customer
For over 50 years, GHH Fahrzeuge GmbH (GHH) has been developing and manufacturing special vehicles for underground mining and tunnel construction - for clients from all over the world. The loaders, dump trucks and mining trucks weigh up to 60 tons, are in use 24/7 and are adapted precisely to the specific requirements of the mine.
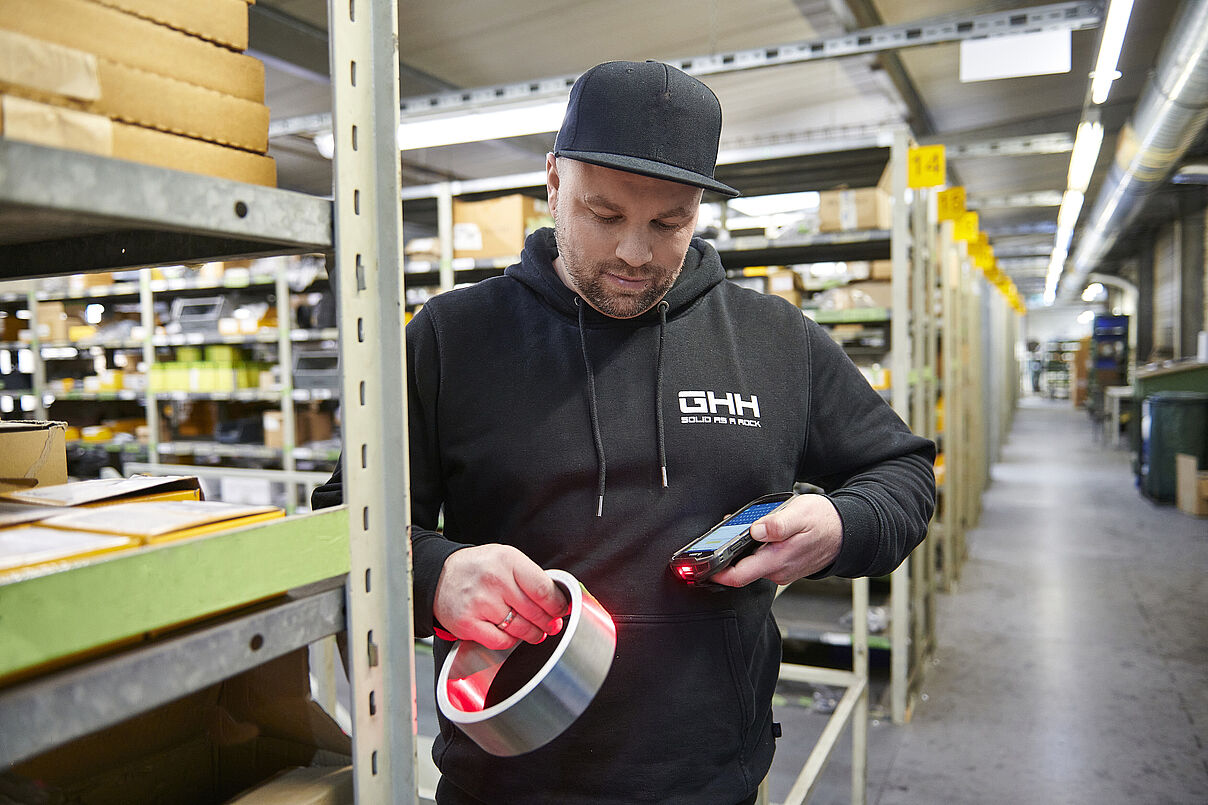
Challenges of the project
90,000 active articles, 40,000 parts lists and vehicles with up to 3,500 parts list items: GHH processes a huge amount of data every day. In view of vehicle delivery times of up to 14 months, the pre-control of key components is also essential for the special machine manufacturer. For GHH, this primarily includes engines, axles and gearboxes, but also steel parts and some valves.
Time-delayed data acquisition
At the end of this chain, all the parts required for a vehicle must be neatly packed at the assembly site. This can only be achieved if information is properly booked through. However, there were still a lot of paper forms and the resulting delays and inaccuracies in the system, both in goods receiving and in the warehouse in conjunction with production. The same applied to shipping. For example, delivery bills were filled out and collected by hand and only handed over to the internal warehouse service after some time. As a result, information was only entered into the system with a time delay. The manual transfer of production numbers or goods receipt documents in particular harbored a high potential for input errors. Sometimes the numbers were transposed, often the writing was smudged or illegible.
Goals of GHH
GHH was looking for a new ERP system that would enable it to efficiently record the multi-layered planning and production data of a special machine manufacturer and significantly increase data quality - as close as possible to the system standard. Manual and paper-based processes were also to be replaced by simple, digital and, above all, time-accurate data capture.
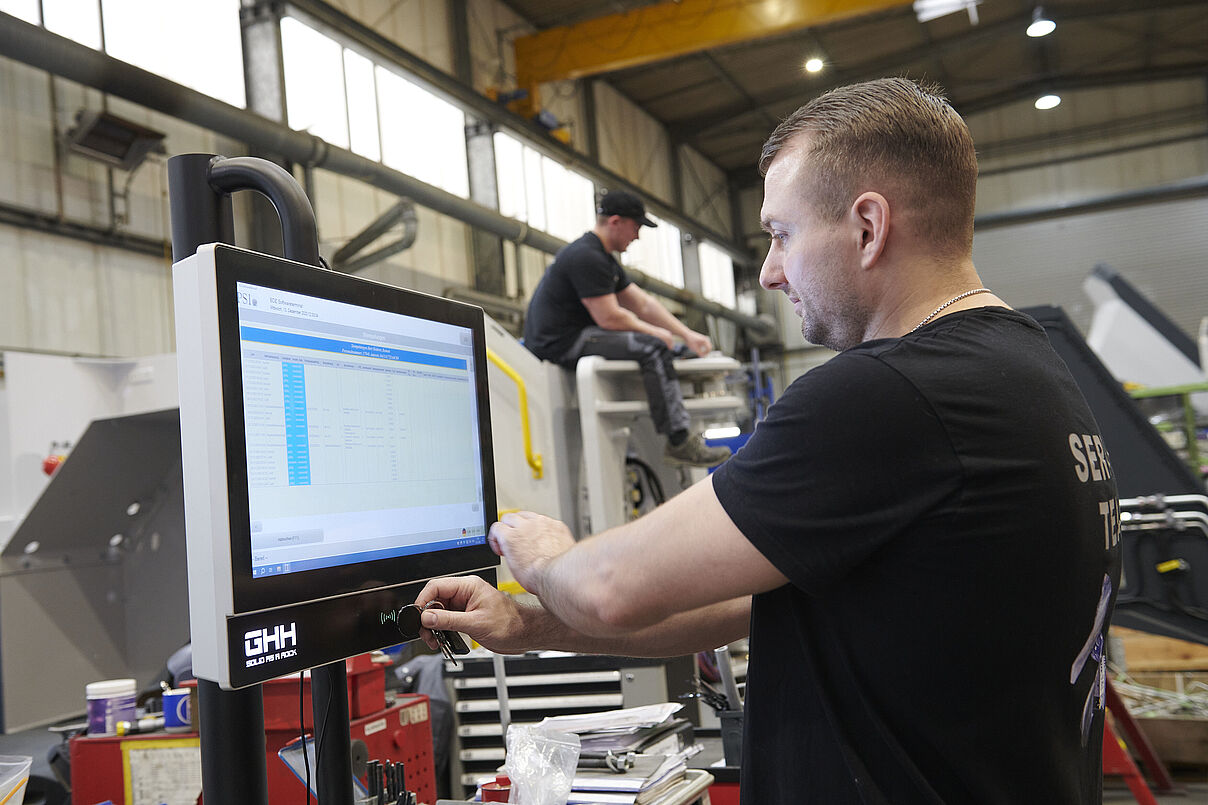
Solution approach
As an industry solution, PSIpenta/ERP and MES already covers numerous GHH processes as standard - including growing parts lists for the pre-control of components. Integrated apps running on scanners are to be used for simple and time-accurate data collection in the warehouse, in goods receiving and in shipping. GHH also followed the PSI project team's recommendation to establish a production and interim warehouse as an additional information level.
Implementation
All operations in the apps, which in principle can include all standard operations from the PSIpenta/ERP client, have been consistently aligned with the respective workflows and the dialogues have been minimized accordingly. All users are only required to provide information from processes with which they are familiar. For example, the warehouse staff scan all goods receipts and record stock movements and material postings directly in the system, including plausibility checks and without any time delay. Input errors are virtually eliminated.
Another important piece of the puzzle on the way to high data transparency is the newly introduced production warehouse including a route-optimized list. Previously, the warehouse staff simply booked out material removed for production. It was then not clear to the workers which material should already be at the workstation, nor where it was located. In addition, the production department only booked unused material back into the system once a vehicle had been completed.
Following the PSIpenta system, the warehouse staff now retrieve the material from the warehouse in a route-optimized manner using the parts lists, book the components into the new production warehouse and immediately print QR codes. This means that each component can also be physically assigned to a production order. The final write-off is then carried out by the production employees. With the production warehouse, GHH has an additional level of information and can also access these stocks if necessary, for example in the event of urgent spare parts inquiries from customers.
Result
High level of identification thanks to proximity to the ERP system - GHH benefits from three key advantages in particular: firstly, data quality has increased massively. Secondly, significantly more information is available, which enables, among other things, a review and improvement of parts list quality. And thirdly, significantly more people are involved in the ERP system.
- massively increased DATA QUALITY
- significantly improved EXPERTISE CAPABILITY
- significantly increased APPLICATION ACCEPTANCE
On the one hand, this increases their responsibility to transfer data correctly into the system, but at the same time it also increases their understanding of how they contribute to the information content. The stronger identification with the new ERP system is also reflected in the high level of satisfaction.
Conclusion
As a special vehicle manufacturer, GHH can map numerous industry processes in PSIpenta/ERP and MES as standard. Not least due to the positive experience with the creation of the production warehouse, the company is already planning to move closer to the standard and thus to processes that contain a great deal of know-how and experience. Thanks to the integration and process-oriented design of the PSIpenta/Industrial apps, GHH has closed even the smallest digital gaps in data collection and is already benefiting from high data quality and transparency as well as high employee satisfaction just a few months after introducing the new system.